From Blueprint to Reality: The Step-by-Step Guide to Custom Metal Building Design
Custom metal buildings have revolutionized modern construction, offering durability, efficiency, and design flexibility for various applications. Whether for commercial, industrial, agricultural, or residential use, metal structures provide a cost-effective solution with faster construction times compared to traditional materials like wood or concrete. From warehouses and retail spaces to prefab homes and storage units, the demand for custom metal buildings continues to rise due to their long lifespan, low maintenance, and energy efficiency.
Designing a custom metal building allows property owners to tailor every aspect to their specific needs, from layout and aesthetics to insulation and sustainability features. However, the process requires careful planning, an understanding of material choices, and adherence to local building codes. Many prospective owners ask, “Can I design my own metal building?” or “How much does a 1,000 sq. ft. metal building cost?”—questions that highlight the importance of budgeting and customization.
This guide walks you through the step-by-step process of designing and constructing custom metal buildings for commercial use—starting from 500 square feet and beyond. Whether you’re planning a retail space, office, warehouse, or other commercial facility, understanding the design and build process is key to turning your blueprint into a fully functional, modern structure.

Step 1: Defining Your Building Needs and Purpose
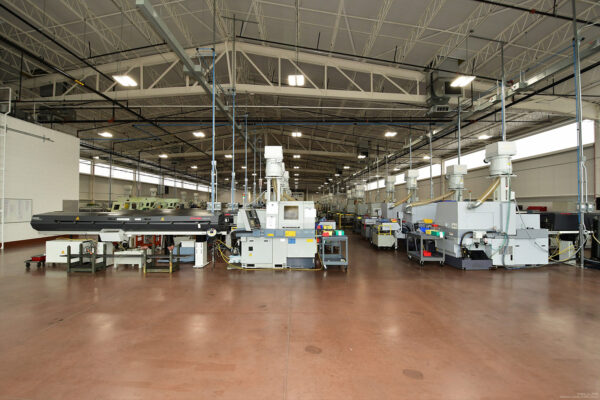
The first and most crucial step in designing a custom metal building is clearly defining its purpose. Whether you’re constructing a commercial warehouse, a retail space, an agricultural barn, or a residential metal home, the building’s function will dictate its size, layout, and features.
Start by asking essential questions:
- What will the primary use of the building be? A manufacturing facility requires different specifications than a storage unit or office space.
- What size and dimensions best suit your needs? A 1,000 sq. ft. metal building may be ideal for a small business, while a 30×40 structure with a concrete slab might suit a workshop or garage.
- What features are necessary? Consider insulation for energy efficiency, ventilation for airflow, or roll-up doors for accessibility.
- Will future expansion be needed? Designing with scalability in mind can save costs later.
Once you define these requirements, you can better estimate costs. While metal buildings are generally more affordable than traditional construction, prices vary based on customization, location, and material choices. By clearly outlining your goals, you ensure your custom metal building is both functional and cost-effective, meeting current and future needs efficiently.
Step 2: Designing Your Custom Metal Building
—
Designing your custom metal building is where your vision begins to take physical shape. This phase goes beyond aesthetics—it’s about functionality, compliance, and long-term performance. During this step, you’ll collaborate with design professionals to determine structural dimensions, roof styles, wall panels, openings for doors and windows, and interior layouts. Factors like your location’s climate, intended building use, and future scalability should also guide design decisions.
Modern design tools, including Building Information Modeling (BIM), allow for precise 3D renderings that help you visualize the final structure. This technology also improves coordination between engineers, architects, and fabricators, reducing errors and construction delays. Sustainable elements, such as insulated panels or passive design features, can be integrated at this stage to enhance energy efficiency.
Designing your metal building with customization in mind ensures it meets your operational needs today—while offering flexibility for tomorrow’s growth.
Step 3: Collaborating on Custom Design and Engineering
—
Custom metal buildings thrive on thoughtful planning and collaboration. At this stage, you work closely with architects and engineers to bring your vision to life through detailed design development. Whether your goal is a sleek modern office, a climate-controlled warehouse, or a mixed-use commercial structure, this step ensures that every element—from spatial layout to structural requirements—is intentional and aligned with your goals.
The design phase includes selecting roof styles, panel types, insulation systems, and energy-efficient features that optimize performance and visual appeal. Meanwhile, engineers assess environmental loads, site constraints, and code compliance to ensure safety and long-term durability. This process results in precise blueprints and digital 3D models, helping stakeholders visualize the final structure before fabrication even begins.
This collaborative design approach not only ensures functionality but also streamlines the next phases of prefabrication and construction. It’s where innovation meets practicality—transforming ideas into engineered solutions.
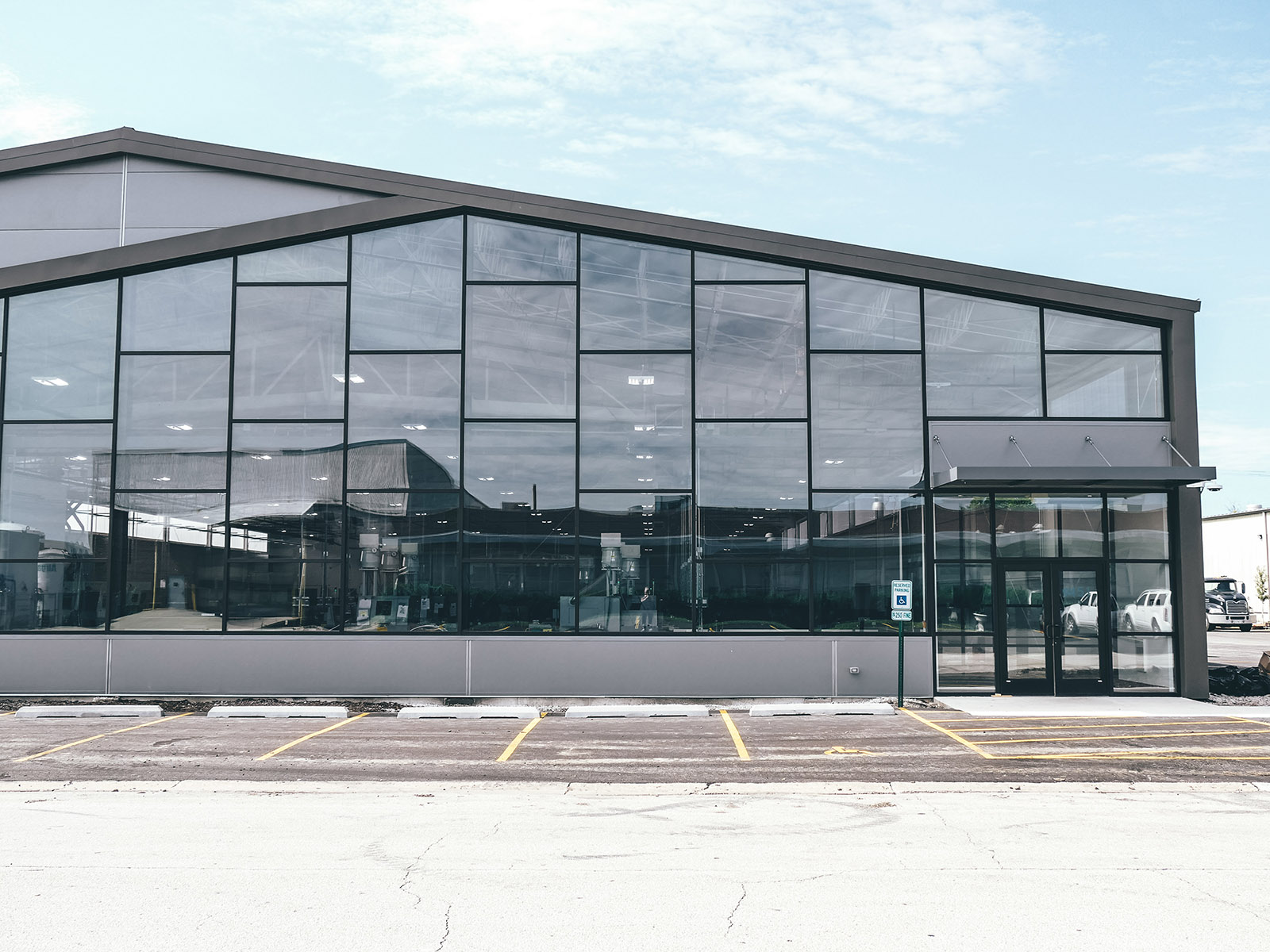
Step 4: Prefabrication and Delivery Process
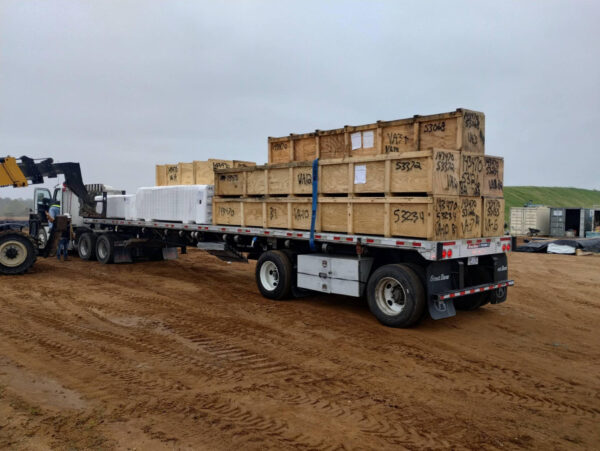
Once your metal building design is finalized, the prefabrication process begins. This stage is crucial as it ensures precision, quality control, and faster assembly. Prefabrication involves manufacturing the building components—such as steel frames, wall panels, and roofing systems—at an off-site facility before they are transported to your construction site.
1. Manufacturing and Quality Control
During the manufacturing phase, advanced computer-aided design (CAD) and CNC machining technologies are used to ensure each component is accurately cut, welded, and formed. This reduces the need for on-site adjustments, saving time and reducing labor costs. The factory environment also allows for strict quality control, ensuring that all components meet high standards before they leave the factory.
2. Customization and Coating
If you’ve opted for custom features, such as insulated metal panels (IMPs), skylights, or fire-resistant coatings, these are added during the prefabrication stage. Many manufacturers also apply protective coatings such as galvanized finishes to enhance durability and resistance to weather conditions.
3. Shipping and Site Preparation
Once fabrication is complete, the building kit is carefully packaged and shipped to your site. Shipping costs depend on location and the complexity of the delivery. To ensure a smooth installation, it’s crucial to have the site properly prepared, including a ready foundation and storage space for the prefabricated components.
By leveraging prefabrication, you can enjoy a more efficient and cost-effective building process with a quicker installation timeline.
Step 5: Assembly and Construction
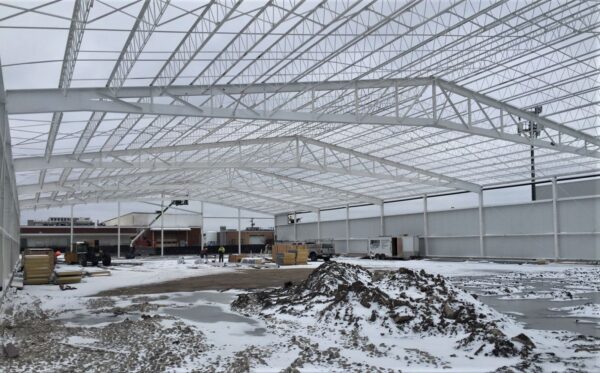
The assembly and construction phase is where your metal building design starts to take shape. Once the prefabricated components have arrived at the construction site, the process moves to the next stage: assembly. This phase is typically faster than traditional construction due to the precise prefabrication of parts.
1. Foundation and Site Preparation
Before assembly begins, it’s crucial to ensure that the foundation is properly laid. A concrete slab or pier foundation is often used for metal buildings, depending on the structure’s size and intended use. Site preparation also includes ensuring that the area is cleared of debris and level, as this directly affects the stability and alignment of the structure.
2. Steel Frame Installation
The first step in assembly is the installation of the steel frame. This includes erecting vertical columns, horizontal beams, and braces that form the skeleton of the building. Steel frame buildings are known for their durability and strength, providing a solid foundation for all other components.
3. Paneling, Roofing, and Final Touches
Once the frame is set up, the next step involves attaching the roofing panels and wall systems, followed by any insulation or custom features. Depending on the design, you may also add windows, doors, and exterior cladding.
Throughout this phase, construction crews ensure that all components are securely fastened and meet safety standards. The assembly process typically takes a fraction of the time compared to traditional building methods, making prefabricated metal buildings a highly efficient construction solution.
Step 6: Final Touches and Inspections
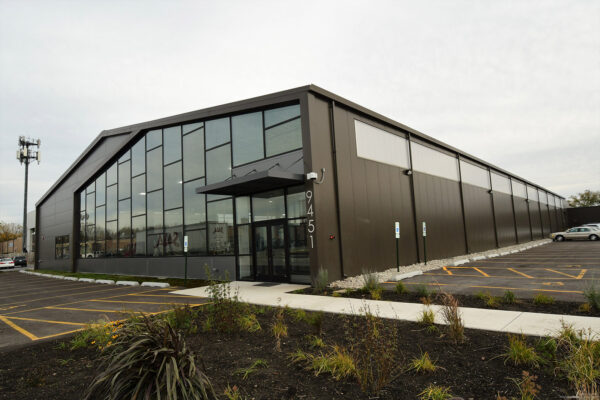
The final touches and inspections phase is critical to ensuring that your custom metal building is not only functional but also meets all regulatory requirements. Once the structure is assembled, the next steps involve completing the interior and exterior finishes, followed by thorough inspections to guarantee safety and quality.
1. Interior and Exterior Finishes
This stage involves adding the finishing touches to both the interior and exterior of the building. For the exterior, this might include painting, cladding, or installing trim for aesthetic appeal and weather protection. On the interior, tasks like installing insulation, electrical wiring, HVAC systems, and lighting fixtures are carried out, ensuring the building is fully operational. Depending on the intended use, custom features such as partition walls, flooring, or specialized equipment might also be added.
2. Safety Inspections
Before the building can be used, it must undergo inspections to ensure it complies with local building codes, zoning regulations, and safety standards. These inspections can include structural integrity checks, electrical system evaluations, fire safety assessments, and HVAC functionality tests.
3. Final Approval
After passing inspections, the building receives final approval for occupancy. This signifies that it’s safe, functional, and ready for use. The building permit is closed, and the building is officially operational.
The final touches and inspections phase ensures your metal building is complete, safe, and ready to serve its intended purpose for years to come.
Conclusion
Designing and constructing a custom metal building involves a careful and systematic process that ensures your vision comes to life with precision, efficiency, and durability. From defining your needs and choosing the right design to navigating the costs, the prefabrication process, and the assembly stages, each step plays a crucial role in creating a functional and long-lasting structure. The final touches and inspections guarantee that the building is both safe and ready for occupancy, providing peace of mind that your investment is secure.
Choosing the right materials, design, and construction partner is vital to achieving the highest quality outcome. At EcoSteel, we specialize in delivering top-notch custom metal buildings that are tailored to your specific needs and built to last. With our expertise and commitment to excellence, we ensure that your project is completed on time, within budget, and to the highest standards.
If you are ready to turn your blueprint into reality and build a structure that is both efficient and resilient, contact EcoSteel today. Let us guide you through every step of the process, providing innovative solutions and unmatched craftsmanship for your next custom metal building project.
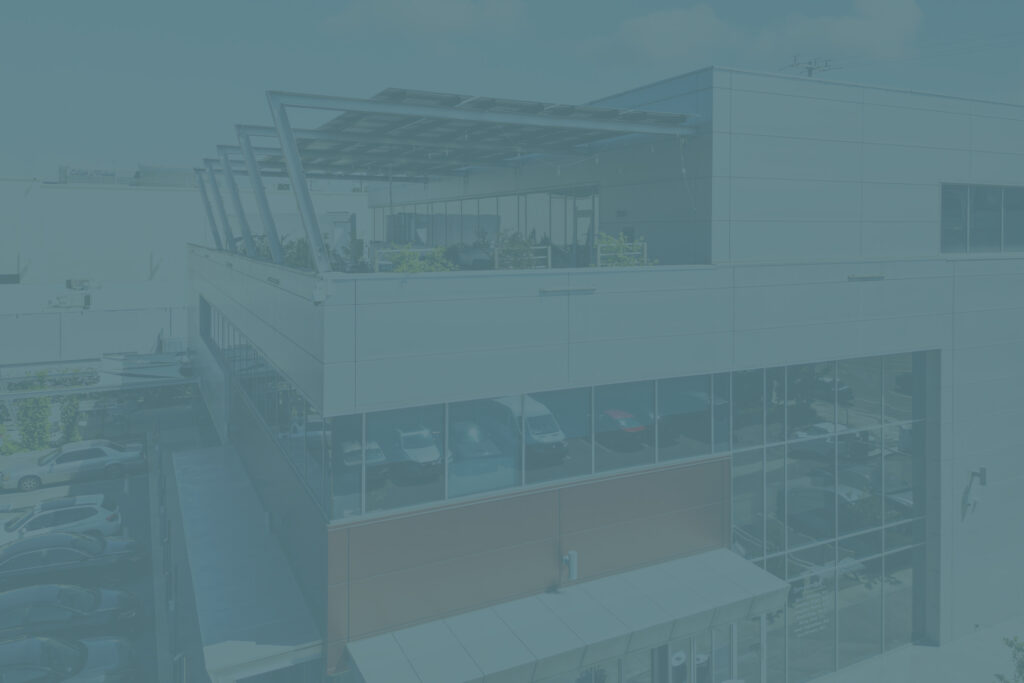
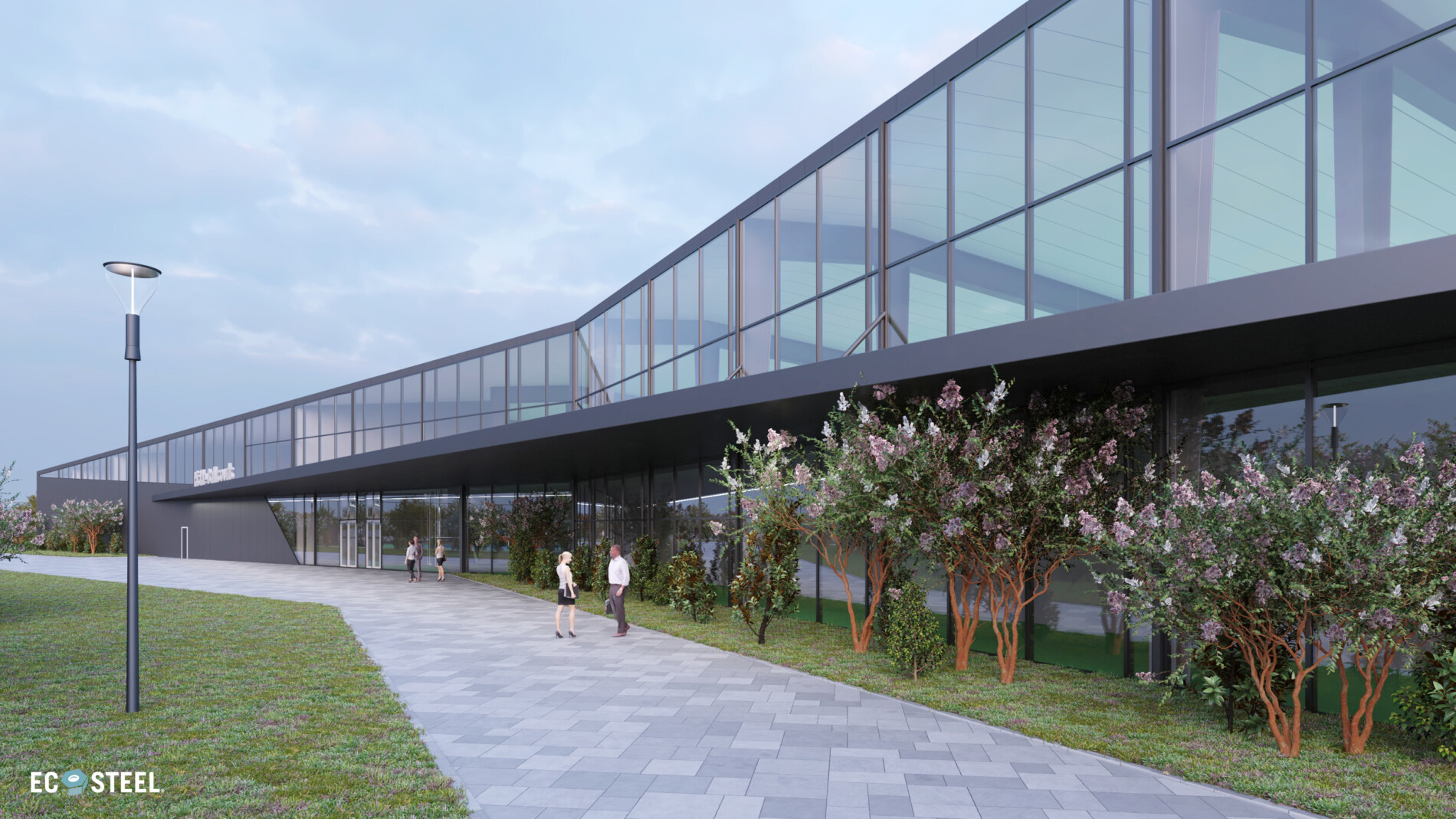
WHY ECOSTEEL?
EcoSteel building systems come in a variety of shapes and sizes, but at their core they all utilize a custom engineered structural steel frame and a high-performance insulated shell. From sub-zero temperatures to dry heat or high humidity, Mother Nature continually tests the limits of building envelopes. While our insulated wall panels are a popular option, sometimes they are substituted or combined with masonry, stone, pre-cast or tilt-up concrete, wood, glass or other architectural wall treatments. The versatility and flexibility of our building systems allows for a myriad of colors, shapes, textures and designs. Today’s building projects require the perfect combination of energy efficiency, creative versatility, and reduced construction cost.
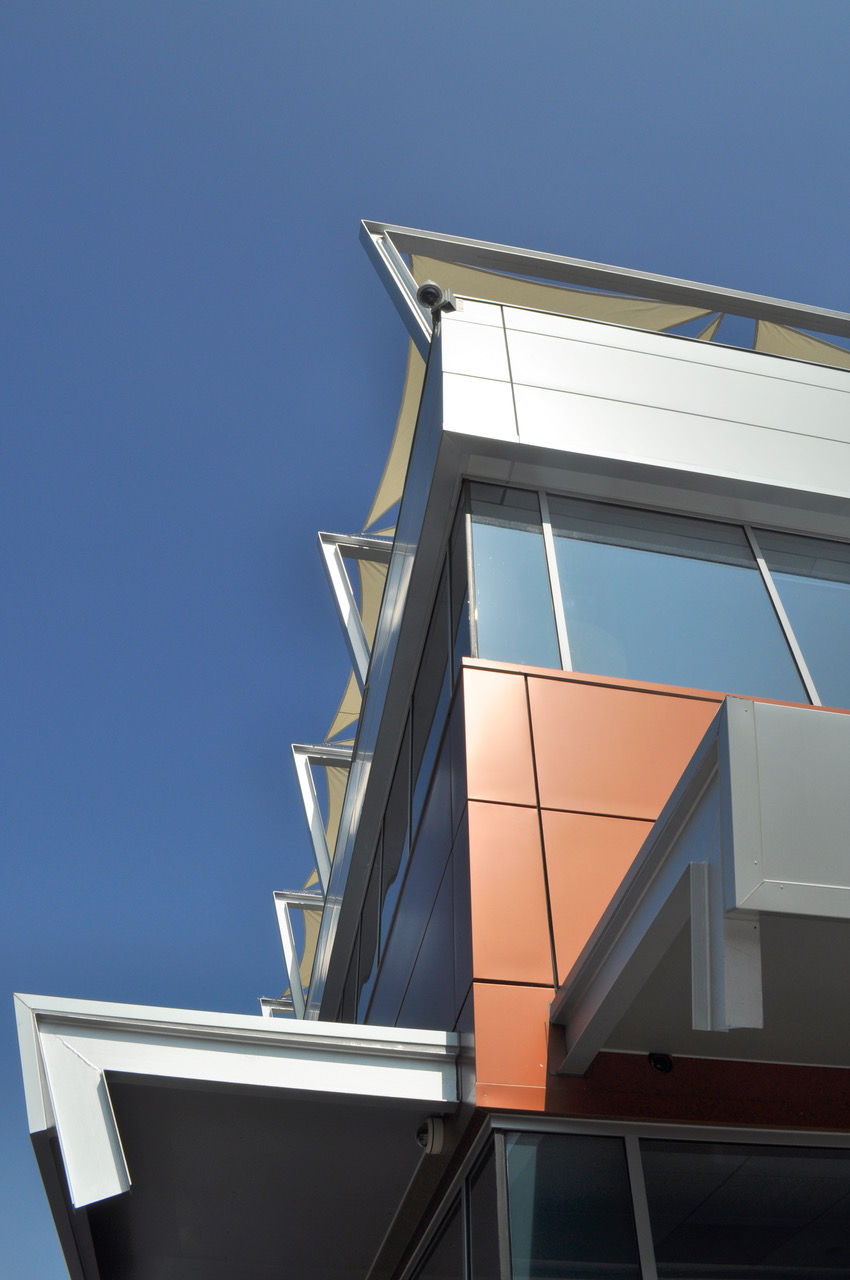
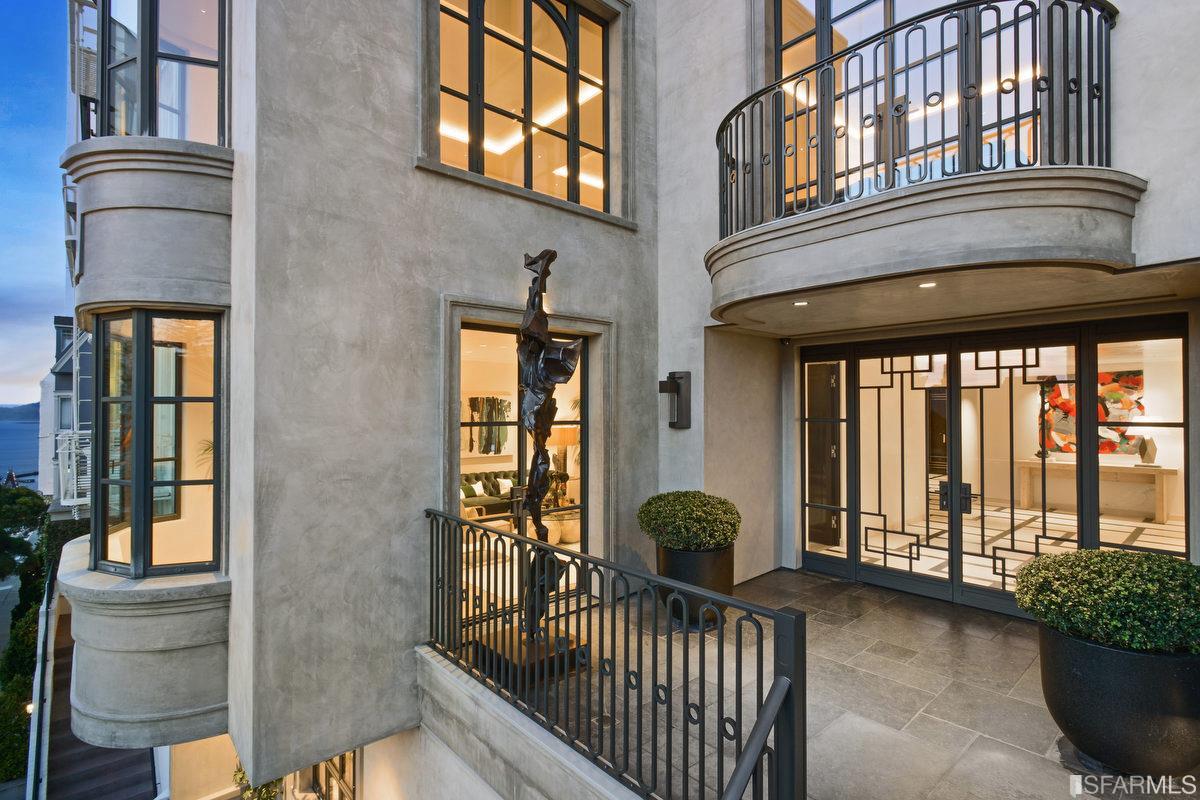
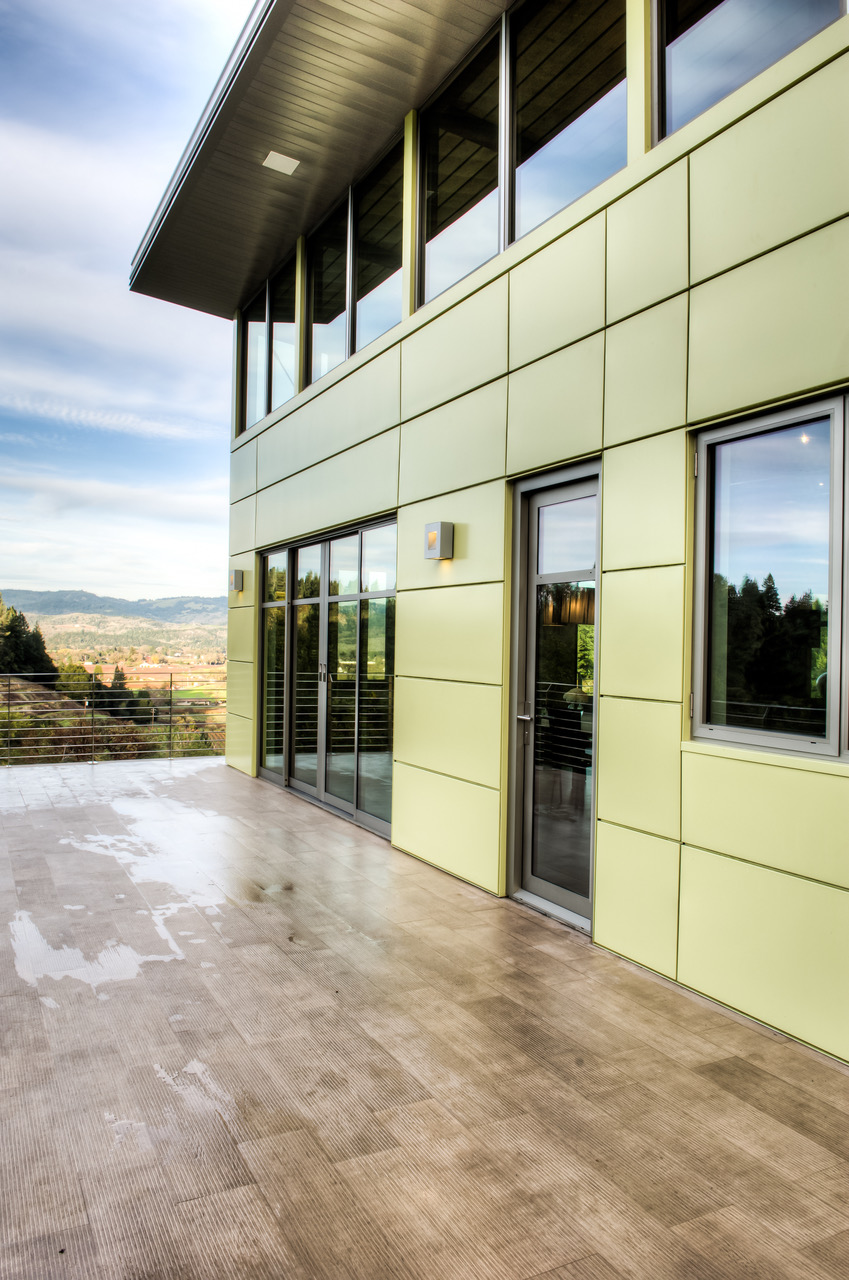
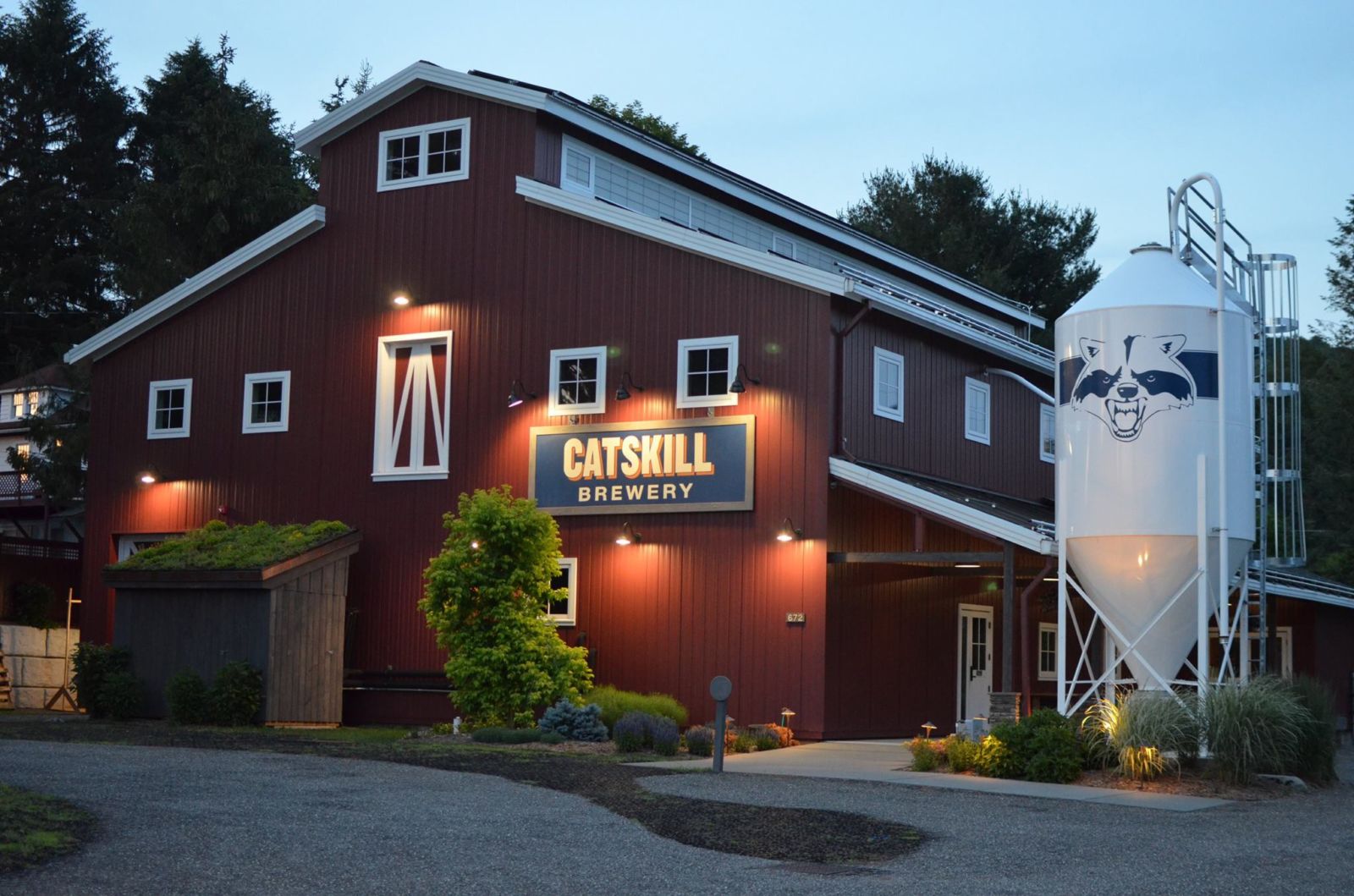
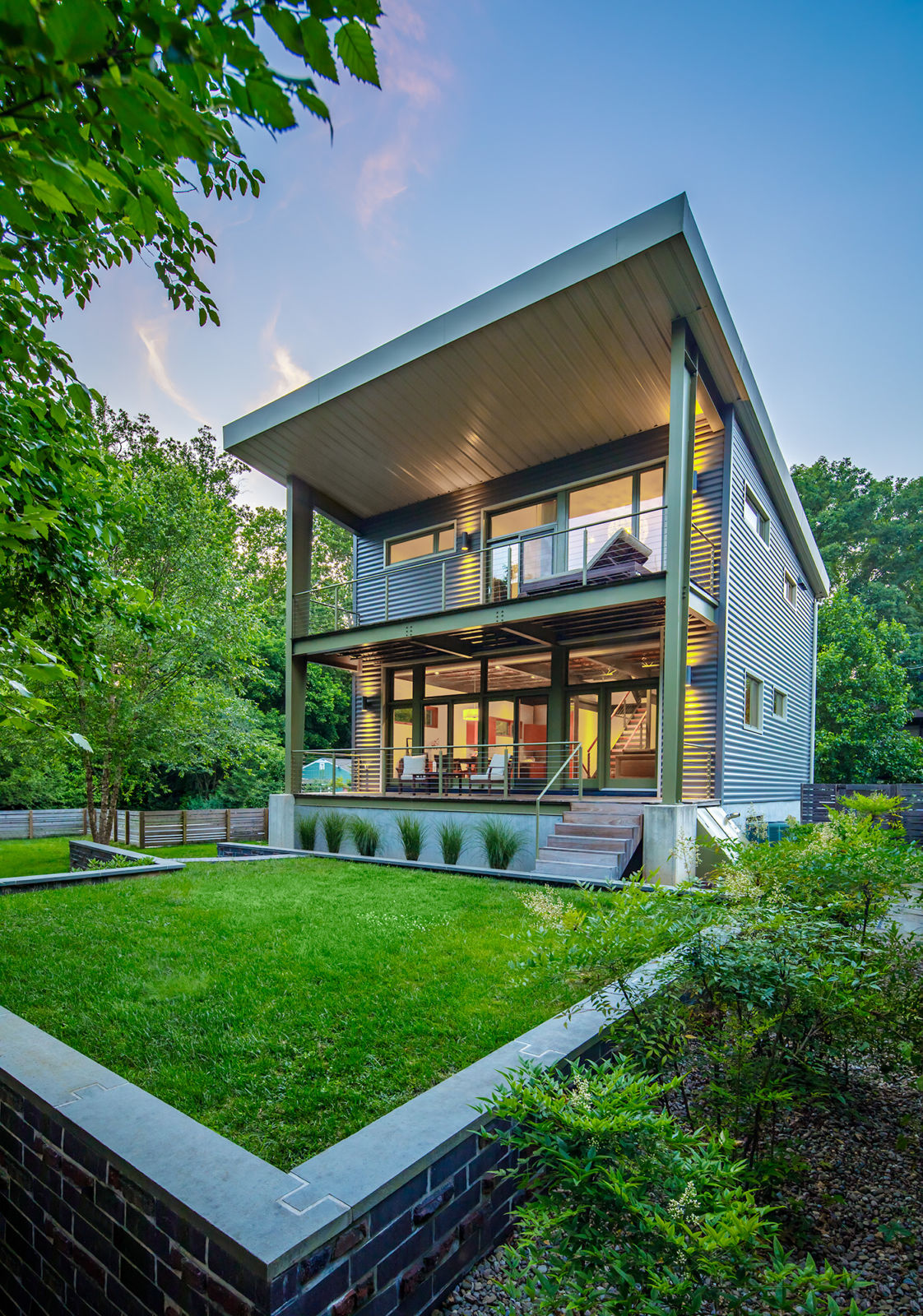
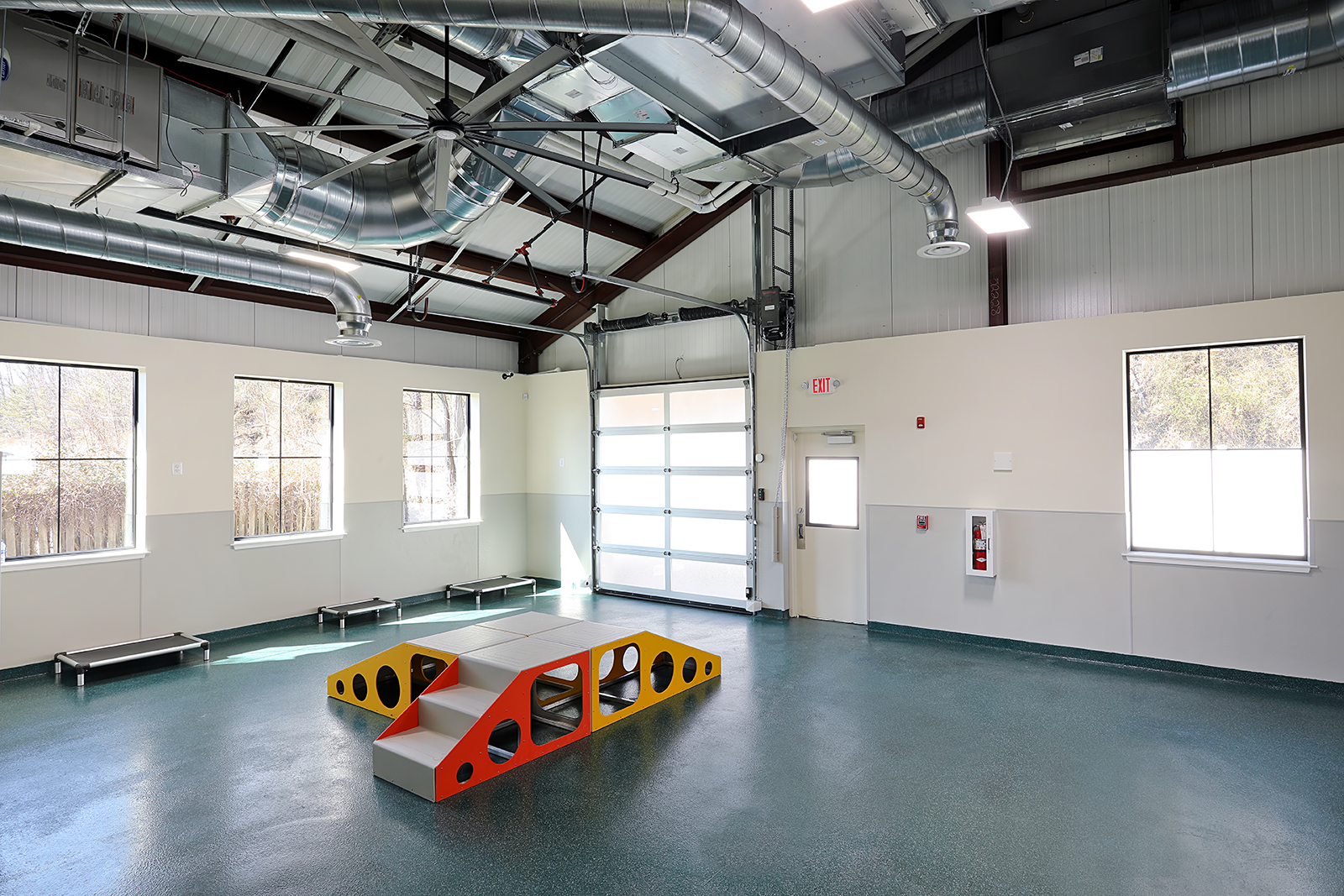
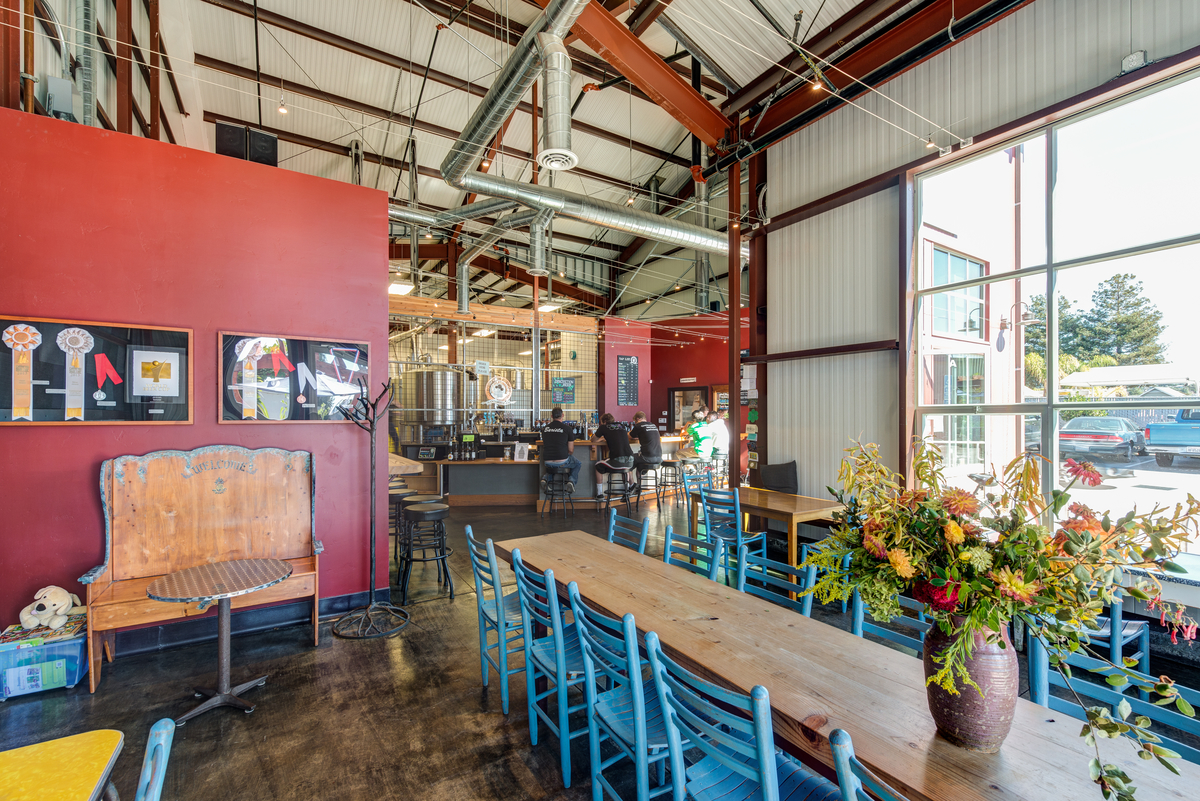
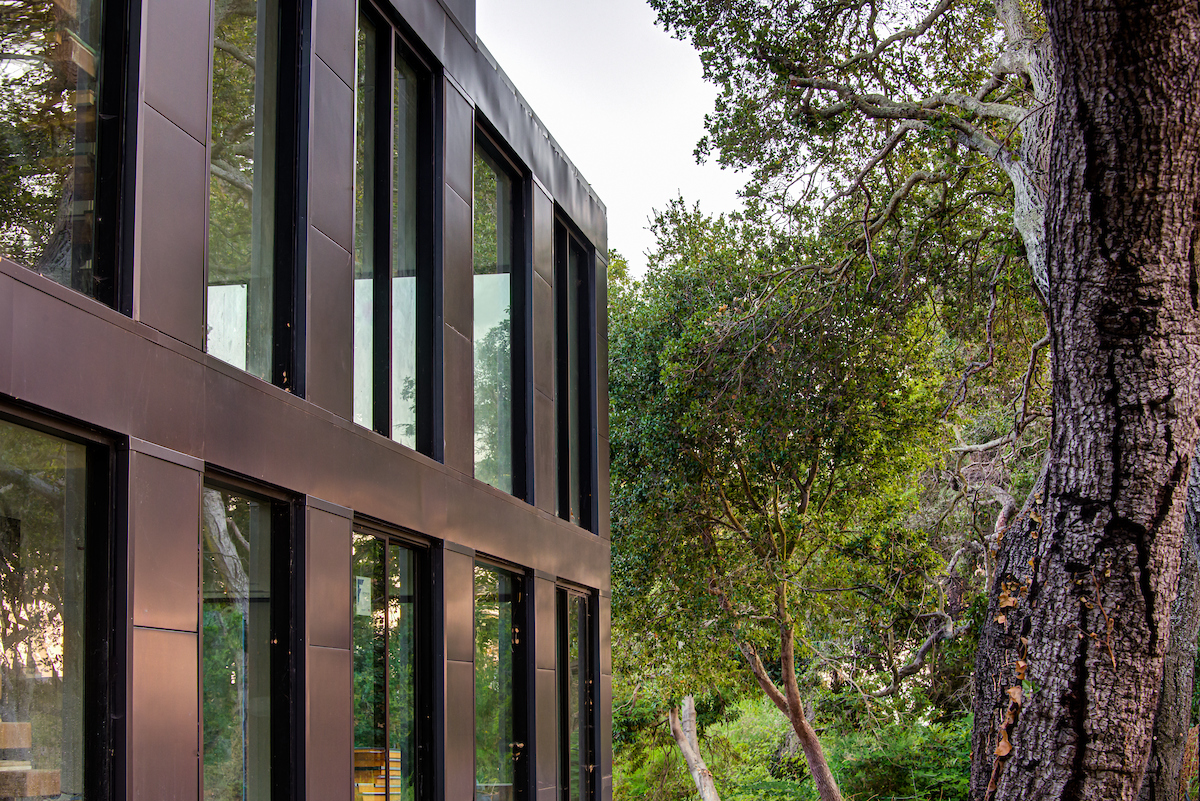
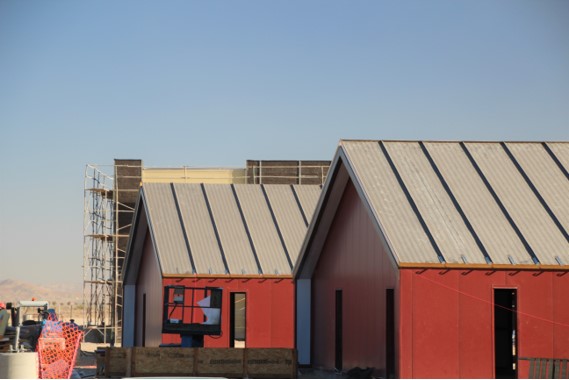
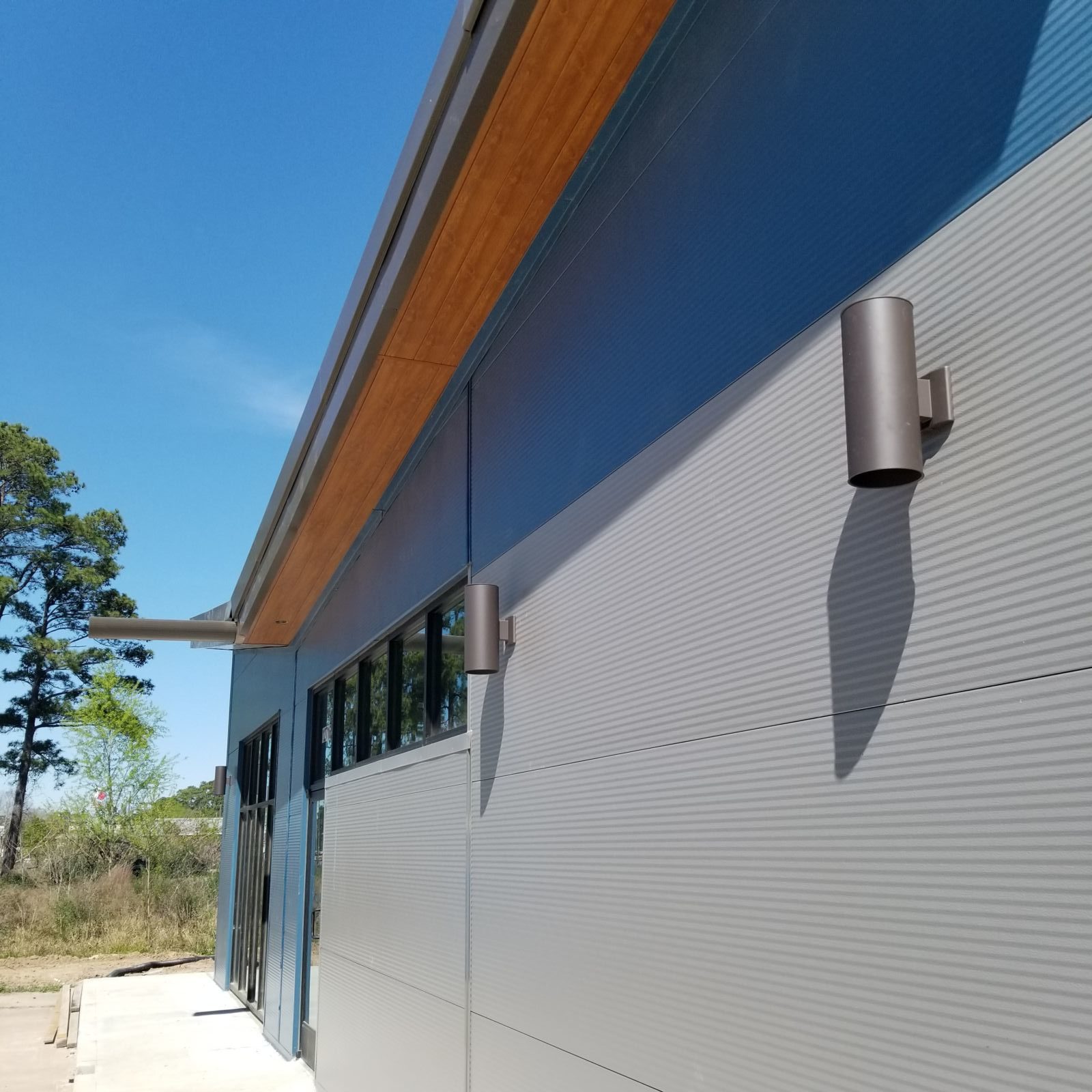

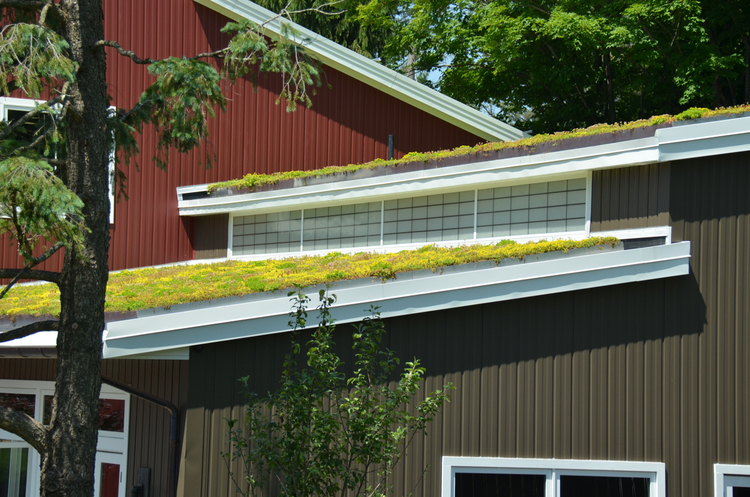
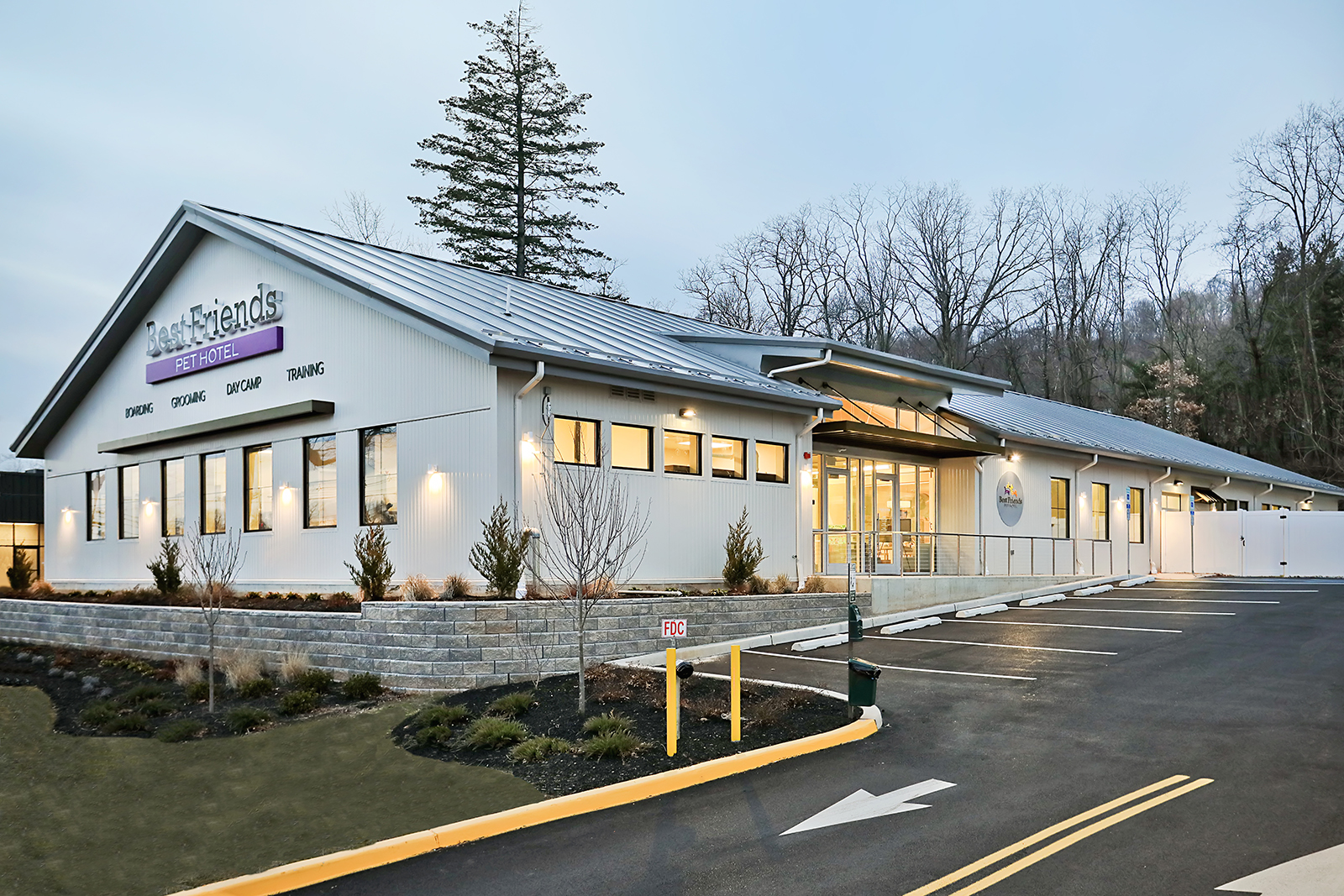
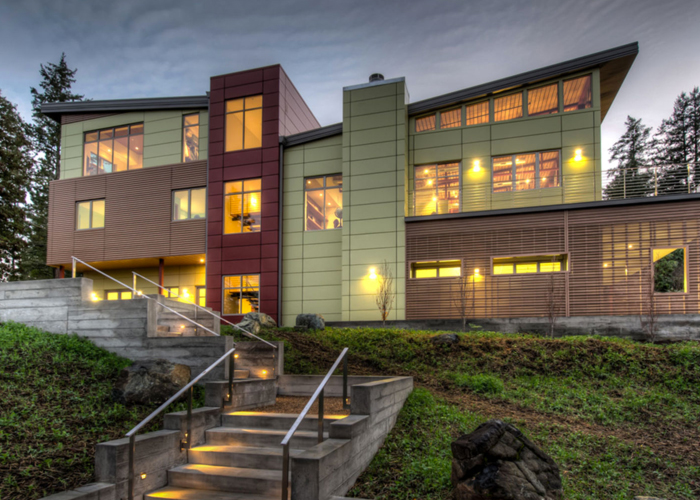
You must be logged in to post a comment.